ДВП, технология изготовления • Транс Лок
Говоря о технологии изготовления такого древесно-плитного материала как ДВП, мы должны рассказать о двух совершенно разных технологических процессах – мокром и сухом методе производства плит. ДВП технология изготовления – достаточно сложный процесс.
Изготовление ДВП
Как изготавливается ДВП – всем интересно узнать. Начнем с сырья для производства ДВП – древесно-волокнистых плит, в основном, это древесная щепа и опилки, которые размалывают для получения однородной массы.
Если способ изготовления будет сухим, то сырье не промывают, а тщательно просушивают. Затем, для связывания мелких частиц, добавляют смолы и другие водостойкие вещества, которые улучшают качество ДВП плит. Сырье настилается сухим ковром на сетку и спрессовывается. Следующим этапом будет раскрой листов, согласно необходимым размерам и, в дальнейшем, еще один этап спресовывания.
Во время сухого технологического процесса количество циклов спресовывания меньше, поэтому и получаемая плотность материала несколько ниже, чем у ДВП, произведенного мокрым способом.
С обратной стороны плиты, произведенные по мокрой технологии, имеют рисунок сетчатого вида, — это еще одно отличие от древесно-волокнистых плит, производимых по сухой технологии.
Нельзя сказать, что какой-либо из способов изготовления ДВП является основным, — все зависит от мощностей производства.
Листовой древесно-волокнистый материал – один из самых используемых древесных материалов и это совсем не древесина, он значительно легче и дешевле, не поддается линейным изменениям, отлично комбинируется с другими строительными плитными материалами, но, в виду невысокой плотности имеет определенные ограничения по установке крепежей.
Древесно-волокнистые плиты, которые производят по мокрой технологии, чаще используют, по сравнению с плитами, произведенными по сухой технологии. Они очень востребованы у мебельщиков, из них изготавливают:
- Полки и обратные стенки различных тумбочек и шкафчиков;
- Днища ящиков в мебели;
- Основания мягкой мебели;
- Всевозможные перегородки;
- Филенки межкомнатных дверей;
- Арочные конструкции для дверных проемов.
Такие древесно-волокнистые плиты очень востребованы у строителей, их используют для изготовления внутренних элементов для обустройства построек в сельском хозяйстве, в автомобильной и судостроительной промышленностях, в производстве различных упаковок – контейнеров и ящиков.
Древесно-волокнистые плиты, произведенные по мокрой технологии, используют во время обустройства полов и как стеновые облицовочные материалы.
Древесно-волокнистые плиты, произведенные мягким способом, применяются в деревянном домостроительстве, при изготовлении межкомнатных перегородок, а также для производства панелей звукоизоляции и утепляющих панелей.
Поделиться с друзьями:
Социальные кнопки для Joomla
Автоматизация производства двп ( мокрым способом)
1. Основные стадии
Процесс изготовления ДВП мокрым способом состоит из следующих основных стадий (рис. 1):
1. Измельчение древесных материалов – получение щепы заданных размеров из древесных материалов (дровяной древесины и отходов деревообработки) путем измельчения их на рубительных машинах (типа МРН-100).
2.
Сортировка щепы – получение кондиционной
щепы заданных фракций древесных частиц
путем
сортирования на сортировке (типа
СЩ-120). Требования
к фракционному составу технологической
щепы: крупная фракция (от 30 до 50 мм) не
более 10 %; средняя фракция (от 10 до 30 мм)
не менее 79 %; мелкая фракция (от 5 до 10 мм)
не более 10%;
менее
5 мм не более 1%.
3. Получение древесной массы 1-ой степени помола – получение древесноволокнистой массы, определенной степени помола (степень помола 14±1 ДС) путем размола технологической щепы на дефибраторах.
4.Разбаление древесной массы в циклоне от 3 % до 34 %.
5. Получение древесной массы 2-ой ступени размола – получение древесноволокнистой массы, определенной степени помола (степень помола 20±1 ДС), путем размола древесной массы 1-ой ступени размола в рафинаторах.
6.
Приготовление
проклеивающих составов – смешивание
в баке
смолы, парафиновой эмульсии, серной
кислоты в заданных пропорциях для
получения клеющего состава с необходимыми
свойствами.
7. Проклейка древесноволокнистой массы – процесс смешивания древесноволокнистой массы с проклеивающим составом, для получения проклеенной древесноволокнистой массы. Осуществляется в ящике непрерывного проклеивания.
8. Формирование древесноволокнистого ковра – получение сформированного древесноволокнистого ковра (и далее пакетов, с помощью пил), осуществляется на отливной машине (типа ХВ-1700).9. Процесс горячего прессования – прессование пакетов ДВП с целью получения спрессованных плит заданной толщины. Осуществляется в прессе.
10. Термообработка древесноволокнистых плит – получение термообработанных ДВП, путем выдержки их в закалочных камерах (2-2,5 часа) для повышения физико-механических свойств.
11. Увлажнения плит – получение увлажненных ДВП, путем выдержки их в увлажнительных камерах для придания формоустойчивости и исключения процесса коробления, за счет достижения влажности плит М=4-10 %
12. Форматный раскрой древесноволокнистых
плит – получение обрезной ДВП.
Осуществляется на форматно-обрезных
станках.
Схема процесса производства ДВП (мокрым способом) представлена на рисунке 1.
Рис. 1. Основные стадии типового процесса производства ДВП (мокрым способом).
1. Анализ участка измельчения древесных материалов в производстве двп мокрым способом.
Целью процесса измельчения древесных материалов является получение древесных частиц (щепы) заданных размеров:
Древесный
материал (бревна) (диаметром до 450 мм и
длинной 1 – 1,5 м по бревнотаске (двигатель
М1) подается в рубительную машину МРН-100
(двигатель М2) (производительность 100
м3 /
ч),
где измельчается в щепу.
При работе вначале запускается двигатель
М1 рубительной машины, а затем двигатель
М2 бревнотаски, что обеспечивает
своевремменую подачу бревен в МРН-100.
Механизмом
резания в рубительной машине являются
вращающийся диск (диаметром 2440 мм.
Рисунок 2 – схема анализа процесса измельчения древесины как ОУ: а) схема материальных потоков и информационных переменных; б) структурная схема САУ.
Описание функциональной схемы
Данная схема предусматривает одну локальную систему управления:
Система предварительного контроля силы резания в рубительной машине. В рубительной машине установлен датчик силы резания C для определения усилия резания (1-1). От него через преобразователь (1-2) сигнал поступает на вход промышленного контроллер, где сравнивается с заданным значением усилия резания (1005).
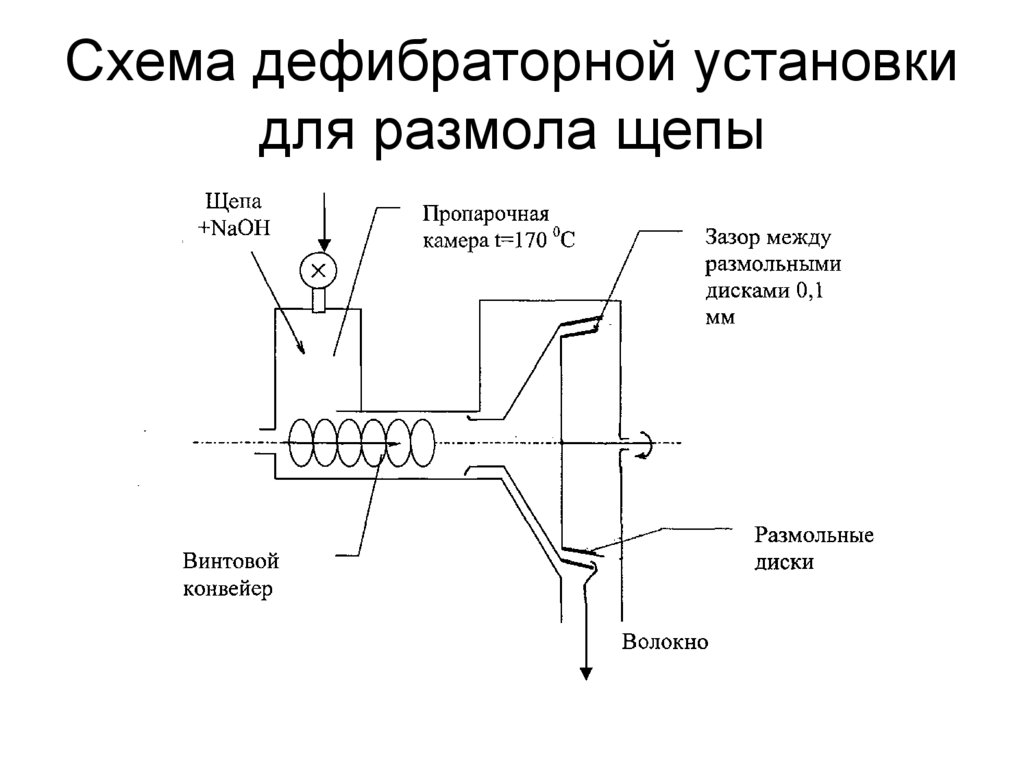
Исполнительный механизм М1 (двигатель бревнотаски) оснащен блоком ручного управления (установлен на щите оператора) для аварийного отключения или включения. Он состоит из элемента ручного воздействия HSA (2-2), пускового устройства NS (2-3) и элементов световой индикации (2-4, 2-5).
Исполнительный механизм М2 (двигатель рубительной машины МРН-100)оснащен блоком ручного управления (установлен на щите оператора) для аварийного отключения или включения. Он состоит из элемента ручного воздействия HSA (3-2), пускового устройства NS (3-3) и элементов световой индикации (3-4, 3-5).
Исполнительный механизм М3 (двигатель ленточного транспортера) оснащен блоком ручного управления (установлен на щите оператора) для аварийного отключения или включения. Он состоит из элемента ручного воздействия HSA (4-2), пускового устройства NS (4-3) и элементов световой индикации (4-4, 4-5).
ДВП означает как мокрый, так и сухой процесс
На рынке древесноволокнистых плит преобладают продукты типа МДФ. Такие изделия обычно изготавливаются с помощью «сухого процесса», что означает, что волокна высушиваются перед формированием матраса, который затем подвергается горячему прессованию. МДФ, однако, является относительным новичком на рынке по сравнению с другими древесноволокнистыми плитами, поскольку самые первые изделия из древесноволокнистых плит были изготовлены с использованием «мокрого процесса», аналогичного производству бумаги, более века назад.
Следовательно, я подумал, что было бы интересно взглянуть на древесноволокнистые плиты мокрого производства, поскольку они являются важной частью наследия сектора древесных плит.
Начальным этапом производства является расщепление древесины на волокна. Большинство продуктов сегодня производятся с использованием термомеханического процесса дискового рафинирования.
В США некоторые фабрики используют пистолет Masonite для парового взрыва горячей древесной щепы в грубые волокна, которые затем очищаются с помощью дисковых рафинеров. Это объясняет, почему оргалит в США часто называют Masonite. Оба процесса разделения на волокна производят волокна с богатой лигнином поверхностью. Это очень важно, так как лигнин играет важную роль в соединении волокон в готовом изделии.
В волокна добавляется много воды для создания разбавленных смесей. Также добавляются другие добавки, такие как клеи, гидрофобизаторы и различные формообразователи. Затем смесь сливают на проволочные сетки с образованием паутины. Дренаж сам по себе не снижает содержание влаги в достаточной степени, поэтому полотна затем прижимаются между валками, чтобы выжать больше воды.
Если фабрика производит древесноволокнистые плиты низкой плотности (<400 кг/м3), часто называемые мягкими или изоляционными плитами, то следующим шагом является сушка полотна в печах.
Рынок мягких досок в последние годы переживает некоторое оживление благодаря моде на плавающие полы, для которых требуется подложка; и к возрождению интереса к изоляционным материалам из возобновляемых источников.
Если, с другой стороны, завод производит изделия из ДВП высокой плотности (>880 кг/м3), то полотна прессуются под высоким давлением и температурой. Полотно имеет высокое содержание влаги 65% и более, поэтому при горячем прессовании образуется много пара. Чтобы обеспечить выход жидкой воды и пара, перед прессованием полотна размещают на сетчатых ситах. Это объясняет, почему одна грань гладкая, а другая имеет отпечаток сетки. Такие панели часто обозначают S1S, что означает гладкую одну сторону. Возможны панели S2S, т.е. гладкие с двух сторон, но перед горячим прессованием полотно должно быть высушено.
Цикл прессования панели S1S предназначен для максимального удаления воды в ее жидкой форме, поскольку сушка панели требует гораздо больше энергии. Таким образом, типичный цикл прессования состоит из трех стадий: начальное и быстрое высокое давление для выдавливания воды в виде жидкости; этап сушки при низком давлении; и, наконец, фаза консолидации от среднего до высокого давления, которая определяет толщину панели.
Затем панели подвергают термообработке, помещая их в печь на два-четыре часа при температуре около 165°C для повышения их водостойкости. Ненасыщенное масло можно наносить на панели перед термической обработкой, чтобы сделать закаленные панели еще более устойчивыми к влаге.
После такого длительного цикла прессования и последующей термообработки панели становятся очень сухими и должны быть повторно увлажнены перед отправкой заказчику. Повторное увлажнение достигается путем пропускания панелей через камеру с высокой влажностью. Панели обычно ставят на край, чтобы обнажить обе стороны и максимизировать поглощение.
Последними этапами производства являются обрезка и упаковка.
С появлением МДФ считалось, что производство ДВП исчезнет, но ДВП выживают благодаря превосходному качеству поверхности – по крайней мере, на одной стороне – и низкому уровню эмиссии формальдегида.
Введение в процесс мокрого твердого картона (WHB)
Мокрый процесс производства твердых древесноволокнистых плит, а также изоляционных плит был введен в начале 1930-х годов. Процесс был изобретен в США и на ранней стадии перенесен в Европу шведской компанией Defibrator AB. Defibrator AB стала играть ведущую роль в разработке и коммерциализации процесса WHB. Компания Defibrator AB со своим основателем Арне Асплундом специализировалась на процессе преобразования древесной щепы в пригодные древесные волокна, а также разработала полный технологический пакет для производства древесноволокнистых плит.
Начиная с 1950-х годов компания Defibrator AB могла поставлять комплектные заводы по производству древесноволокнистых плит, включая технологии, от древесного склада до готовых древесно-волокнистых панелей. Для таких комплектных поставок завода Defibrator AB сотрудничала с другими шведскими поставщиками оборудования, такими как Söderhamn для мокрого формования, Motala Verkstad для горячего прессования, Svenska Fläkt для термообработки и увлажнения и Mohög для обработки и резки панелей.
В период с 1950 по 1990 год более 100 линий по производству древесноволокнистых плит мокрым способом были доставлены в места по всему миру.
Компания Sunds Defibrator, которая стала OEM-поставщиком после приобретения таких ключевых игроков отрасли, как Defibrator, Motala Verkstad и Svenska Fläkt, долгое время занимала лидирующие позиции на мировом рынке в этой области. Позже Sunds Fibertech AB приобрела права интеллектуальной собственности и теперь является OEM-поставщиком. Эта технология по-прежнему очень конкурентоспособна благодаря своим преимуществам, заключающимся в отсутствии смолы и уникальном качестве картона.
Базовая технология процесса На фоне истории, описанной в Части 1, легко понять, что технология, используемая в производстве древесноволокнистых плит мокрым способом, хорошо себя зарекомендовала и надежна. Процесс основан на трех основных этапах:
• Преобразование древесной стружки в волокно
• Формование непрерывного мата из влажного волокна
• Прессование мата из влажного волокна при повышенном давлении и температуре.
Эти основные этапы процесса оставались неизменными на протяжении многих лет разработки. Однако изменился размер и эффективность используемых компонентов машин.
Типичный уровень производительности производственной линии в 1950-х годах составлял лишь около 75 т/день по сравнению с сегодняшними линиями производительностью более 300 т/день.
Однако объем производства всегда будет ограничен форматом горячего пресса с точки зрения размера плиты и количества отверстий для прессования. Выбранный размер плиты часто кратен коммерческому размеру платы 4 фута на 8 футов.
В дополнение к увеличению размеров, важное развитие произошло в таких областях, как более эффективный процесс производства волокна, а также улучшение общего контроля и мониторинга процесса. Это привело к снижению энергопотребления и сокращению выбросов загрязненной технологической воды, а также к сокращению количества персонала.
Выбор сырья и подготовка щепы
Большинство видов древесной щепы подходят для производства ДВП. Однако используемая порода древесины будет влиять на качество конечного продукта из ДВП.